Design errors when designing gravity smoke removal systems for buildings
The list of design sins is long and sometimes surprising. Which of them occur most often?
Ewa Karczewska, Coordinator of the Design Department in the Smoke Extraction Division of MERCOR S.A.: Indeed, the number of design errors in the field of smoke removal installations, as well as their diversity, is quite large. From the perspective of the Coordinator of the Design Department in the Smoke Control Division, I encounter various types of situations that are consulted and corrected by our team of designers.
I think that errors in construction designs that are transferred to the detailed design often result from the fact that they are made by people with limited knowledge in the field of designing smoke removal systems.
An example of a common error is assuming that the active surface area of devices is too small or too large without justification. Another case is the implementation of a smoke removal installation without an executive design, only on the basis of the PB, preliminary assumptions or CFD analysis. Speaking about the analysis itself, it is also worth mentioning the problem of recognizing that CFD analysis is able to justify all, even the most sophisticated, departures from the design assumptions.
Unfortunately, inappropriate design standards or practical assumptions are often adopted, e.g. assuming the height of the smoke layer covering the stored goods, which is contrary to the idea of using the system, i.e. the so-called property protection.
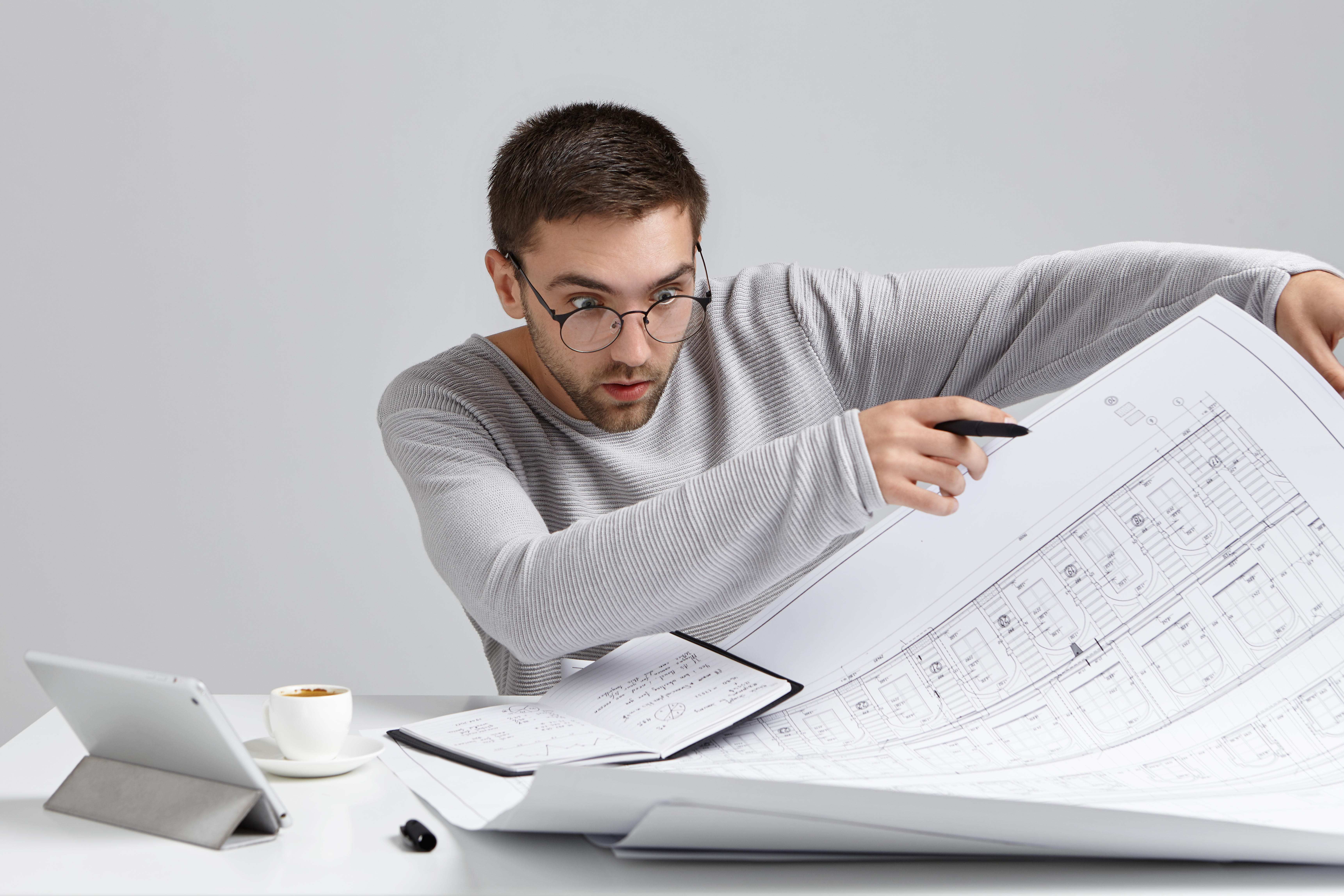
Does it happen that the design of the smoke removal installation does not meet the basic requirements included in the design? How should designers maintain consistency between the construction design and the technical and executive design?
Ewa Karczewska: A construction design is often treated as a basic study that must be created in order to obtain a building permit. Unfortunately, companies often treat it as a source of knowledge about a given system, which is a wrong approach. A construction design usually contains basic information about a given system. If they are correct and the pre-selected devices meet the requirements, it may be the basis for the implementation of a technical or executive design, but the executive/technical design is intended to indicate properly selected solutions, supported by calculations, a detailed description of the installation and cooperation with other installations.
What is the role of taking into account the sprinkler system and its interaction with the smoke exhaust system, as well as other installation elements in the facility? What can result if these two types of fire protection are not reconciled?
Ewa Karczewska: The basic issue is the designer's awareness of the percentage of active smoke removal area for buildings not equipped with a sprinkler system at a different level than for buildings equipped with such an installation. In facilities not equipped with a sprinkler system, the fire power, and therefore the mass of smoke generated, will be much higher than in facilities equipped with automatic water extinguishing devices, which translates into the above-mentioned active smoke removal area. The coordination of the above-mentioned systems is also important, because failure to coordinate the sprinkler installation design with the smoke removal design in terms of overlapping the boundaries of sprinkler sections with the boundaries of smoke zones may result in the opening of more smoke zones than indicated.
In addition to the lack of coordination of the smoke removal project with the sprinkler installation, inconsistencies often also concern other designed elements or devices that may obscure the opening of smoke flaps - e.g. roof structure elements, ventilation ducts. These types of elements should be analyzed in relation to the designed system. It also often happens that air handling units or photovoltaic panels on the roof prevent full opening of the flaps in the event of a fire. Therefore, joint inter-industry coordination is important from the beginning of the design process, which will slowly avoid the above-mentioned problems.

What is CFD analysis and why do you need to do it? Who can come to the aid of a designer who has no experience in doing so?
Ewa Karczewska: CFD analysis is a development that most often complements the design of a smoke removal system. Its implementation allows you to assess the system's operation based on the previously prepared model and the established conditions and assumptions. The analysis is particularly important when the project contains atypicalities and deviations from the standard requirements due to a non-standard situation.
On the other hand, the problem is also the treatment of CFD analysis as a "cure" for all deviations from the norm, which I mentioned at the beginning. CFD analysis should be performed by a person with special preparation and experience. Due to the large amount of details, determining specific parameters and the need to correctly create a reference model, it cannot be a random person.
Every company dealing with smoke removal projects should have in its human resources a suitably prepared person/s who perform such analyses. As part of our activities, at MERCOR S.A. we are able to help clients perform this type of analysis, giving them confidence that it is done correctly.
Many design problems, and therefore the risk of making mistakes in the design of fire protection, concern warehouse and production buildings, including high-bay warehouses. Which standard can help solve these problems?
Ewa Karczewska: Design standards available on the market, with appropriate knowledge and interpretation, are the right direction. However, it is worth supplementing the so-called technical knowledge acquired during various types of industry training.
Design problems most often result from insufficient experience in the design of smoke removal/fire protection systems as well as from incorrect interpretation of the provisions in the standards. In such a case, it is recommended to consult specialists in this field: system designers and fire protection appraisers who will help in finding the right design path.
The most common problems I encounter due to lack of knowledge and poor interpretation include:
Taking too small an active smoke exhaust area for warehouse facilities - the reason is discrepancies in the so-called "high storage",
• Adoption of too short smoke curtains dictated by the investor's requirements due to the so-called free space, e.g. at the bottom of the structure,
• Adopting fire rate coefficients that are inappropriate for the material stored in the facility/smoke zone and/or inconsistent with the tabular data included in the design standard,
• Determining the lower level of the smoke curtain in relation to the height at the ridge, and not the average height of the building/smoke zone,
• Incorrect assumptions in the case of calculations regarding the area of make-up air (so-called aeration).
How can MERCOR help designers and protect them from making mistakes and thus encountering problems during the acceptance of buildings?
Ewa Karczewska: MERCOR, as a company with extensive experience in the industry, helps already at the initial stage, i.e. in preparing the correct concept of the smoke removal system. The design department also deals with the verification of projects created outside our scope, as well as the preparation of complete projects in the mentioned scope.
Additionally, we share our knowledge. We prepare training in installation design (also dedicated to a given organization/company after prior notification and arrangement of details). We also support you in the preparation or prepare CFD analyzes yourself, based on the knowledge and experience of the best specialists in the industry.
Thank you very much for the interview and I wish you as few design errors as possible to correct!
Interview by: Izabela Adamska, Marketing Project Coordinator at MERCOR S.A.